Building a better inspection process is essential for any business. It can help you catch problems early and prevent them from becoming bigger issues down the road. By following these tips, you can create a system that works well for your business and helps you avoid costly mistakes.
Section 1: Create a System for Inspection
To ensure that your products are meeting the quality standards you set for them, it is important to have a system in place for inspection. A well-organized inspection process will help you identify and correct any problems before they become serious, and it will also help ensure that your products are consistently meeting your standards.
One of the key elements of a successful inspection process is good documentation. Keeping track of what was inspected, when it was inspected, and what findings were made can help you pinpoint any areas where improvement is needed. Additionally, using standardized forms or techniques for documenting inspections can make tracking and reviewing each step easy.
Section 2: Use Technology to Help You inspect Better
Technology has been proven to be a valuable tool in the inspection process. By using technology, inspectors can save building inspections cost and time while providing a more accurate inspection. Some common technologies used in the inspection process include digital cameras, laser scanners, and thermography.
A digital camera is an excellent tool for taking photos during the inspection process. They are small enough to be carried around easily, and they produce high-quality photos that can be used for documentation or for training purposes. Additionally, digital cameras are able to capture images in low-light conditions, which is an important factor for inspections that take place during night time or inside buildings with limited light availability.
Training inspectors on how to properly inspect a building can help keep them safe and prevent costly mistakes. Proper inspection includes verifying that the building is structurally sound, checking for proper maintenance, identifying any potential hazards, and issuing appropriate warnings or citations.
One way to train inspectors is to provide them with documentation of proper inspection techniques. This can include guidelines from the National Fire Protection Association (NFPA) or other similar organizations. Additionally, training sessions can be conducted using interactive tools such as video lectures or online simulations.
It is important for inspectors to be properly trained in order to avoid making errors that could lead to serious consequences. By following proper inspection procedures, buildings will be safer for everyone involved and may result in fewer fines levied against property owners.
Section 3: Have Frequent Inspections
Frequent inspections are a key part of maintaining quality control in any manufacturing process. By inspecting the workflow and processes regularly, you can identify and correct any problems before they become major issues. Here are some tips for effective inspections:
1. Make sure all employees are aware of your inspection policy and procedures.
2. Conduct inspections throughout the manufacturing process, not just at the end. Inspections at various points in the process can help to detect problems early on, when they’re more manageable.
3. Use automated tools and equipment to help with your inspections. This will save you time and help you keep track of progress throughout the process.
4. Follow up on any findings from your inspection visits by taking action (e.g., issuing a warning, making changes to procedures.
Building a better inspection process is not difficult, but it does require some effort. By following the tips in this article, you can create a system that will help you avoid the extra cost of building inspections and ensure that your buildings are in good condition.
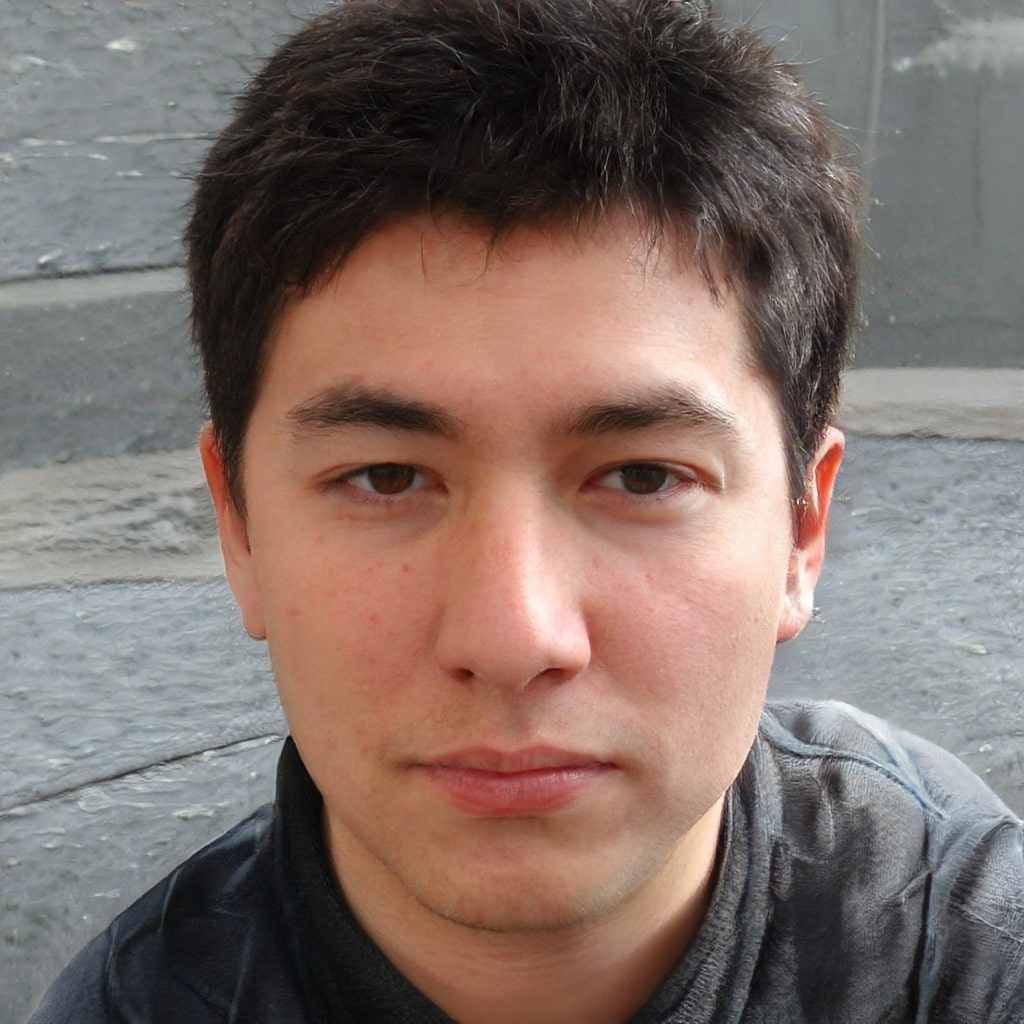